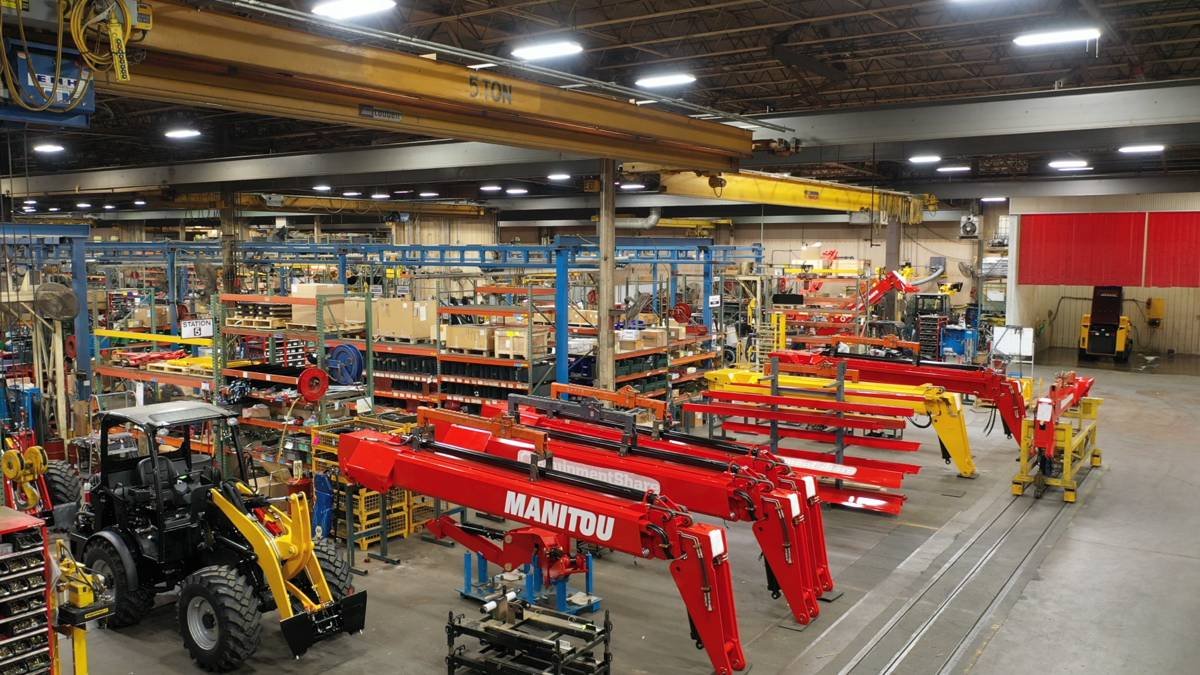
Ergonomic Assembly System for Heavy-Duty Forklift Telescopic Masts
Context & Need
In the manufacturing of heavy-duty telescopic masts for large forklifts (3.5-ton capacity), precise assembly and handling are critical to ensuring structural integrity, reliability, and safety. These masts, essential for lifting and maneuvering heavy loads, consist of three interlocking sections, along with hydraulic cylinders and cable chains, which must be precisely positioned and secured during assembly.
Traditional manual handling of such large components poses several challenges:
High physical strain on operators, leading to fatigue and potential injury.
Difficulty in achieving precise alignment, which can result in assembly errors and rework.
Safety concerns, as operators may need to work under suspended loads, requiring strict compliance with lifting and workplace safety regulations.
To address these challenges, a specialized assembly system was required—one that could support, position, and secure the mast sections while ensuring operator safety, ergonomic working conditions, and improved assembly efficiency.
Developed Solution
To facilitate the safe, precise, and efficient assembly of heavy-duty telescopic masts for 3.5-ton forklifts, a customized assembly system was developed. The solution integrated a dual-head positioner capable of handling up to 8 tons, combined with a tailor-made support cradle designed to hold, align, and secure the three mast sections during assembly.
By allowing operators to work in an ergonomic and controlled environment, this system significantly reduced physical strain, improved positioning accuracy, and enhanced overall safety, ensuring compliance with lifting and workplace safety standards.
-
As an industrial lifting system, the machine had to meet strict safety and certification requirements. Close collaboration with Bureau Veritas ensured compliance with:
CE 2006/42 (Machinery Directive) for lifting equipment.
ISO 13849 for safety-related control systems.
EN 13155 for lifting accessories and risk reduction.
A full structural analysis and risk assessment were conducted, focusing on load stability, failure scenarios, and operator safety, ensuring that the system could operate without compromising structural integrity.
-
The support cradle between the two positioning heads was designed as a mécano-soudure (welded structure) to achieve the required strength-to-weight ratio while maintaining precision alignment of the mast sections. Key design elements included:
High-strength steel beams with reinforced joints to withstand dynamic forces.
Precision-machined mounting points for repeatable and accurate positioning.
Adjustable locking mechanisms to hold the mast securely during assembly.
This custom-built cradle played a critical role in ensuring the proper fit and function of the telescopic sections while resisting mechanical stresses during handling.
-
Given the 8-ton lifting capacity of the Lambert & Jouty dual-head manipulator, extensive finite element analysis (FEA) and structural calculations were required to validate deformation, fatigue, and load distribution.
Load simulations revealed stress concentrations in key areas, requiring design modifications.
Near-limit calculations meant extensive iterations to optimize the safety factor while maintaining functionality.
Deflection and rigidity studies ensured that the mast sections remained aligned throughout the process.
This phase was crucial to ensuring reliability, as the results were pushed to design limits, requiring careful reinforcement and real-world validation.
-
The Lambert & Jouty positioner used for this project consisted of:
Two parallel rotating heads, allowing precise angular and height adjustments.
Independent servo controls, ensuring synchronized motion and fine-tuned positioning.
Heavy-duty clamping and securing systems to prevent slippage under load.
The manipulator was key to reducing operator fatigue and improving safety, as it allowed for ergonomic positioning of the mast at each assembly stage without requiring excessive manual handling.
-
Replacing the existing system required a two-week installation phase, including:
Dismantling the old machine while ensuring minimal production downtime.
Mechanical assembly of the new system, including structural anchoring and alignment.
Electrical and hydraulic integration, ensuring seamless control operation.
Final validation and operator training, with functional and safety tests.
The successful on-time deployment of the new assembly system ensured a smooth transition and immediate production improvements, with enhanced ergonomics, safety, and efficiency.
This highly specialized assembly solution now plays a key role in improving the precision and productivity of telescopic mast manufacturing, while ensuring full compliance with industrial lifting and safety regulations.
Results & Impact
The custom lifting and positioning system revolutionized the assembly of 3.5-ton telescopic forklift masts, delivering significant gains in safety, precision, and efficiency.
✅ Full Compliance with Safety Regulations – Certified by Bureau Veritas, the system meets CE 2006/42, ISO 13849, and EN 13155 standards, ensuring safe operation in a lifting environment.
✅ Ergonomic and Secure Assembly – The dual-head manipulator and custom cradle reduced operator fatigue and manual handling risks, improving working conditions.
✅ Optimized Positioning and Alignment – The high-precision design enabled flawless integration of mast sections, hydraulic cylinders, and cable chains, reducing assembly errors.
✅ Engineered for Heavy Loads – Extensive structural calculations and reinforced welded construction ensured reliability despite near-limit stress conditions.
✅ Successful Deployment with Minimal Downtime – The old system was removed and replaced within two weeks, allowing for seamless transition and immediate production improvements.
This high-performance assembly solution now plays a critical role in increasing production efficiency, ensuring worker safety, and maintaining the highest quality standards in heavy-duty forklift mast manufacturing.
The projects and images presented on this site illustrate projects I contributed to during my previous professional experiences or projects completed with zaKraft. They aim to showcase my skills in design and project management. These machines are not offered for sale by zaKraft.